ECS-1200 Control System by HF Controls
ECS-1200 - Powerful, Scalable Distributed Control System
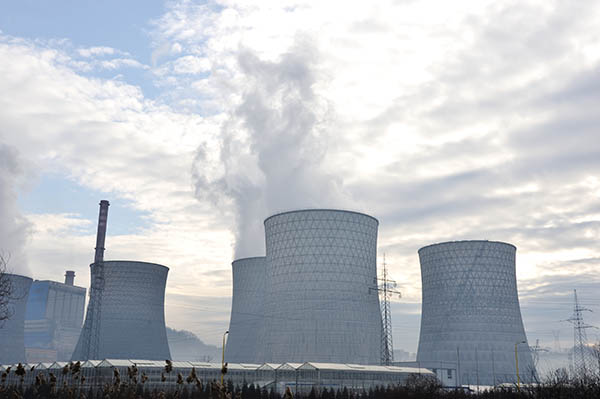
A powerful, yet scalable system with superior reliability and flexibility, the ECS-1200 distributed control system is the result of more than five decades of innovation and manufacturing of control systems with hundreds of installations around the world.
With scalable architecture to match any size control requirement, each system provides complete, fully integrated network and system control solutions in any application or industrial setting.
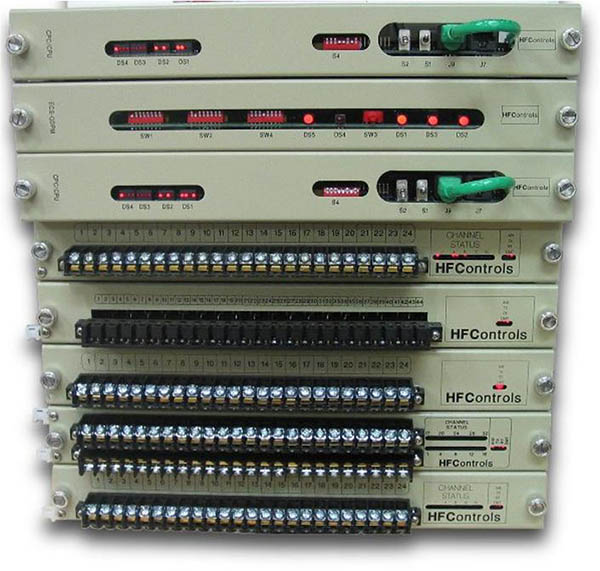
Encompassing an extensive selection of I/O cards for the simplest to the most complex operations, the ECS-1200 control system is fully redundant for confident operation during critical control conditions. Linked through a high-speed, open architecture network, the advanced microprocessor-based control system can perform all sequential and modulating control functions including plantwide data acquisition, monitoring, and display functions with superior integrity and maximum data throughput. With the open architecture network, connection of foreign devices and third-party software applications is easily achieved. Reduced integration time and hardware costs eliminate communications cables and dramatically improve configuration flexibility and maintenance facility.
The ECS-1200 distributed control system consists of five major components: Multifunction Controllers, Input/Output (I/O) modules, Applications Software, Industry Standard Communication Networks, and the Advanced Operator Interface Workstations. These components combine to deliver an exceptional process automation solution that not only optimizes plant performance and efficiency, but also is an extension of management's daily decision making tools.
COMPONENTS
Controllers
A high-performance processor can be found at the heart of every ECS-1200 controller. In addition to the advanced CPU, high-speed sequence control and continuous control can be achieved on the same controller, improving handling capacity and speed. For even more fail-safe control functions, HFC offers an optional redundant configuration on all controllers, allowing bumpless transfer of control during any situation for maximizing plant uptime. Each controller also incorporates self-diagnostics on startup and during execution resulting in outstanding reliability. HFC offers the following controllers designed to meet your process control needs:
Q-Series I/O Modules
The ECS-1200 Q-series I/O modules are remarkably intelligent. The advanced microprocessors prevent system failure by providing internal fault detection through redundant communications links. Memory, calibration, communications status and critical diagnostic information are continually checked and relayed back to the controller for faster resolution of plant process control problems within the system and in the field.
The Q-series I/O modules also features onboard signal conversion for direct connection to field equipment with a wide range of electrical characteristics. This feature eliminates the need for external interposing relays or other signal conditioning hardware, reducing the overall cost of the control system.
The I/O modules can be configured to predetermined failure modes to protect plant assets. Data integrity is completely assured with unique error-checking and communication subroutines. Heavy-duty card-edge bezels provide direct connection to field wiring simplifying both system installation and post installation troubleshooting. In addition, all outputs are individually fused and surge suppressed to meet or exceed IEEE 472-1972 (ANSI C37.90).
Applications Software
The ECS-1200 applications software library contains functional analog and digital algorithms designed for process control. A modular, high-level control application editor includes predefined control functions and also supports customized solutions to meet plant needs. The editors are based on the Microsoft® Windows® operating system. A simulation mode is available for employee training and system testing purposes.
ONE-STEP Automated Logic Generator
The ONE-STEP® graphical configuration software package enables the use of AUTOCAD® for complete control system configuration. This graphical, icon-based system configuration tool translates CAD drawings and compiles function blocks into executable code. Plant engineers can create and modify control logic application codes of a loop controller in a completely graphical based programming environment. System configuration and maintenance are extremely user-friendly and allow minimal operator intervention and manual configuration.
ONE-STEP® can create a dynamic data image of a CAD drawing related to the logic inputs and outputs, all while operating online with the loop controller. The data image can be output to a high-resolution workstation monitor providing an interactive analysis tool for use by operations staff.
Function Blocks
Analog applications are constructed from predefined analog algorithms called function blocks. Various blocks are then linked together to produce the composite algorithm for the process, and the resulting output controls the AO channel to the field device. The anti-windup feature in the control blocks provides bumpless transfers when control or operating modes are switched. Because this protection has been built into the block algorithms, the user is not required to set up external feedback and tracking schemes to prevent controller windup.
Alarm Management
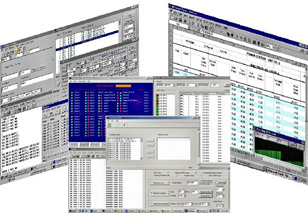
The CRT software provides a dynamic tool for alerting and troubleshooting process limits. The interactive graphics are highly configurable with a range of functions, colors, and display settings for constructing each alarm point. To optimize productivity, alarms can be configured differently for operator versus engineering workstations and even per HFC system database. Graphic displays can be defined to prioritize alarms and automatically suppress alarms for defined process conditions. Alarm analysis and reports can be generated from the historical archiving system to identify alarm trends and areas of improvement for increased efficiency.
Communications Network
The HFC communications network is the most flexible network available today. The network accepts all systems and devices including PLC and CEMS and can support commercial software in addition to HFC software. The redundant communications links between the controllers provide exceptional data integrity and stability. The redundant 10/100Mb/sec C-link allows the connection of multiple controller units and distributed control is supported through high-speed fiber optic links to form an extremely well designed and reliable communications network. For interface with our advanced CRT operator and engineering workstations, high-speed, open architecture technology provides a 100Mb/sec TCP/IP local area network (LAN). Communications gateways and switches enable easy connection to multiple workstations as well as allow secure access to plant control operation from offsite locations.
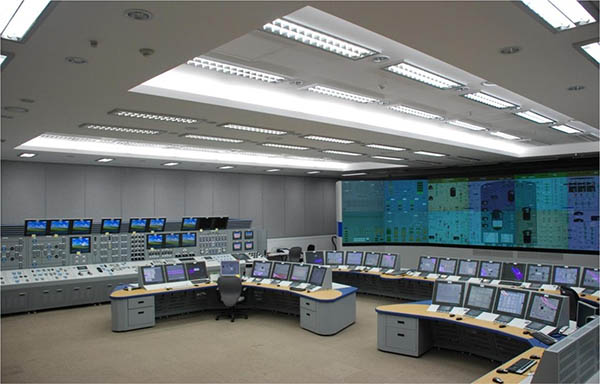